Antique Cast Iron Toys – All About Making, Buying, and History
Antique Cast Iron Toys – All About Making, Buying, and History
For those that don’t know, back in the EARLY 1900s, and late 1800’s toys were made of iron. YES, hit your kid brother, heavy cast iron toys were a thing. All the cool kids had a toy the heft of a hammer and could maim each other, gouge mom’s wood flooring, and crack toes.
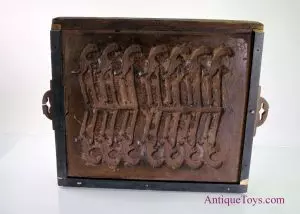
Iron Mold by J.E. Stevens
How Antique Cast Iron Toys Were Made
Cast iron was an early and relatively easy way to make toys in the industrial age. Toys were designed by making wood carvings; easy. The carved patterns were put in sticky sand molds; sort of easy. Great wood patterns produced great toys, so smoothness and detail mattered!
Then molten steel was poured in; EXPERTS only here. The sand mold was ready with impressions from the wood. Gates, or channels were needed in the mold to allow metal to flow (see the picture above).
Finally, depending on the complexity, companies could get slave, ahem, cheap labor from women and children to assemble & paint the toys. -Just sprinkle in non O.S.H.A. conditions. Kids and Women often painted toys one after the other for 9 to 10 hour days with lead paint and long animal hair brushes for exacting details.
Most antique cast iron toy were then riveted together. Axles were fitted with wheals and then crushed, or peaned at the ends. Hubley used one axle end pre-made with a button head rivet. Arcade Toys often heat cut and crushed/finished ends.
Antique Cast Iron Toys Are Heavy
These Iron toys tended to be heavy and required help from steel towns (think Pennsylvania and Ohio areas), and required trains. Trains were the preferred way to ship the heft to distributers aka “jobbers”. Jobbers tended to be in St. Louis, New York, Chicago, and relatively proximate locations. Throughout the history of iron toys, one can see attempts to lighten the toys. Thin early castings saved material and shipping weight. Cutouts and holes allowed the same and gave the toys an artistic look. Open hood vents were Truly open to the air. Trunks, hoods, and panels often got lightening holes. Sheet metal truck beds were even used.
Antique Cast Iron Toys Manufacturers and Makers
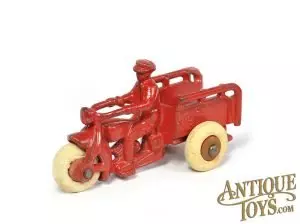
Hubley Motorcycle Toy
Hubley Toys of Lancaster, PA was a juggernaut of toy prowess and ability. “They Just Look Real” according to their ad, and we would agree. Hubley put in creases in the clothing, added studs to the motorcycle metal tires, executed flesh colored paint, and added a nice gloss of pant and stickering.
Kenton Toys of Kenton, Ohio was a smaller and highly artistic company. We see iron elephants, camels, Dewey emblazened cannons, horses, cars, trucks, etc; but these were made with an extra fine sand detail. Paintwork was quite thin, but well applied.
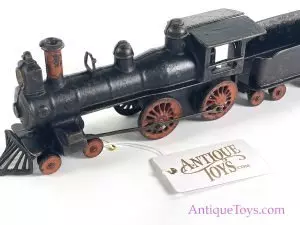
Wilkins Cast Iron Train with Tender
Wilkins of NH made some of the best Cast Iron Trains. Be sure to check out some of their work in person, and you will nary notice a grain of sand showing. The trains and horse toys (another of their specialties) were expertly cast in the northeast late 1800s.
A.C. Williams on the other hand went the route of Walmart. They chose cheaper price points and volume, volume, volume. Certain cars and AC Williams trucks are all over because they were popular for kid budgets. Be sure to look up a Willaims race car or large Lincoln though. This same company would throw down the gauntlet in design from time to time. AC Williams did a great job hitting different price points, and as a result, also spanned a big range of quality and carving/casting details.
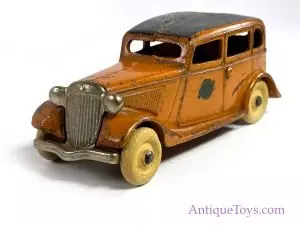
Beautiful Arcade Toys Ford Sedan with Sticker
Any conversation or article on cast iron must include the iconic brand of Arcade Toys. This Freeport, IL company made some of the best iron cars and trucks period. Arcade had a more premium branding and size, so the company worked on realism and painted detailing. They sticker their toys with pride and often cast in or “signed” their work. Arcade taxi cabs began the craze, then Andy Gump Toys and trucks. Later Model A toys, planes, tanker trucks, car carriers, and delivery vans worked into the lineup. Be sure to contact us if you have a boxed or high condition Arcade toy. We would love to see details and can help grade it &, if necessary, adopt it out.
One must be cognizant of other brands out there– Freidag, Shimer, Ives, JE Stevens, Harper (England), S&O, Grey Iron, Tom Sehloff, Motorcade, Jones & Bixler, plus. We can help unravel the mystery if you need identification help.
In case collectors feel that reproductions will hurt the market, NO, they will not in our opinion. Fake or modern iron tends to be poor or costly. To make a quality iron toy you need a foundry to start. Most are extinct or don’t do small batches. One must know the proper alloys and metallurgy for composition. One needs to know the proper temperature to pour and maintain proper flow. Artists need very difficult to find sand; then the adhesive inside. One needs perfect carvers to make perfect patterns. One needs cheap labor, cheap transportation, and affordable price points. Don’t forget the paint which tends to have a bit of bad chemicals and lead to “flow out properly” -Get the camel hair brushes too and belt sanders and….. well, one gets the picture. Cast iron toys are hand carved, hand poured, hand detailed artistic items. Art is expensive, and other materials are a cheaper evolution of toys.
Pick up a bootleg cast iron toy and one can see a grainy appearance from poor sand quality. One can note they are heavy and crudely thick. Paint jobs are usually poor. Details tend to be “soft” rather than crisp and exacting. Etc, etc, etc. See our Youtube video on REAL versus FAKE iron toys for details.
Hopefully this helps you appreciate cast iron toys. We love them! We can help with your collection or inheritance or insurance valuation. Be sure to share details at toys@antiquetoys.com
Best Regards,
Ed
P.S. We also buy cast iron toys and can help with auction options too!
.